Frozen Food Palletizing
Designing highly effective and efficient palletizing systems for frozen food applications requires added levels of ingenuity, skill and experience related to special suits, enclosures and components.
Key Elements of Robotic Food Palletizing
From specialized suits to protect the robots to unique designs that automate every process while utilizing very little space, developing frozen food robotic palletizers is as much of an art as it is a science.
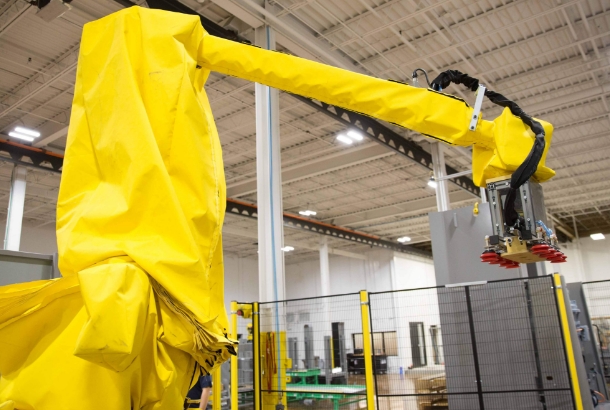
Protective Suits for Robots
Frozen environments require us to integrate heated suits that eliminate problems associated with frozen and blocked airlines while keeping the robot operating at an optimal level.
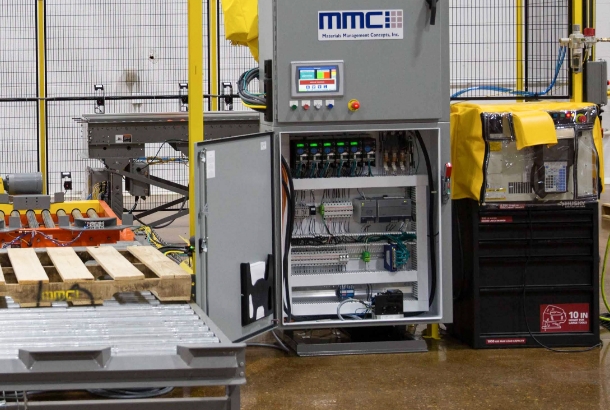
Special Enclosures
We typically enhance the electrical and pneumatic components with special enclosures, heaters and other components to compensate for sub-zero conditions and give operators full control over the system's temperature.
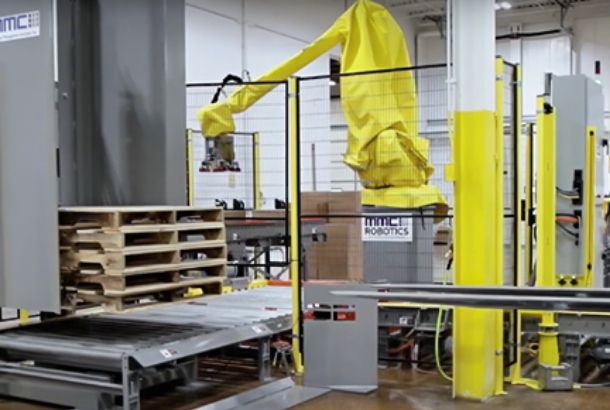
Complete Automation
Minimizing human exposure to the freezing area often involves the automation of the pallet dispensing and discharging processes.
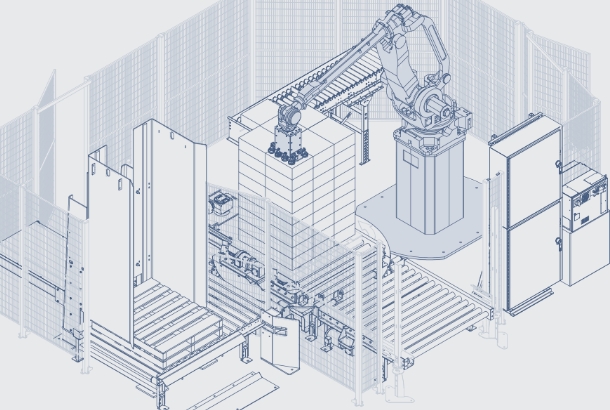
Small Footprint
Given the high costs associated with maintaining such a low temperature in a facility, frozen food palletizers typically require a a design with a small footprint.
A Case in Point
See how we worked with one of the largest food companies in the world to automate palletizing in a raw meat processing facility.