Bakery Supplies
Rethinking Processes & Installing Intelligent Software Yields Major Savings
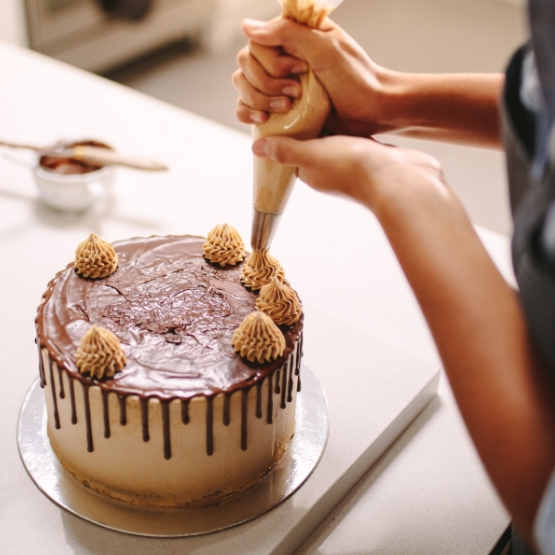
The Client & Objective
As one of the nation’s leading suppliers of bakery products, our client stocks more than 5,000 products in its Midwestern distribution center and proudly promotes itself as THE one-stop shop for bakeries and cake decorators across the country.
Our client partnered with MMCI Order Fulfillment to conduct an on-site design study, asking, “Is there a better way to pick using our current hardware and warehouse management software?”
The Challenge
Shipping around 4,000 orders on an average day, our client had to balance orders from large retailers like Walmart with small-quantity orders from independent bakeries. There was currently one system employed for all orders and it used large totes that severely congested the existing conveyors.
Then: Congested & Gridlocked Conveyors
Now: KPIs Reduce Wait Times & Prevent Gridlocks
Next, there was no system for specifying shipping containers and warehouse personnel - under pressure to get orders out the door as fast as possible - were choosing larger-than-required shipping containers for most orders. They wanted to avoid the possibility of having to repack an order if the initial shipping container selected was too small. However, this inefficient packing logic led to shipments dimensionalizing which increased shipping costs drastically when multiplied by the large number of orders being processed.
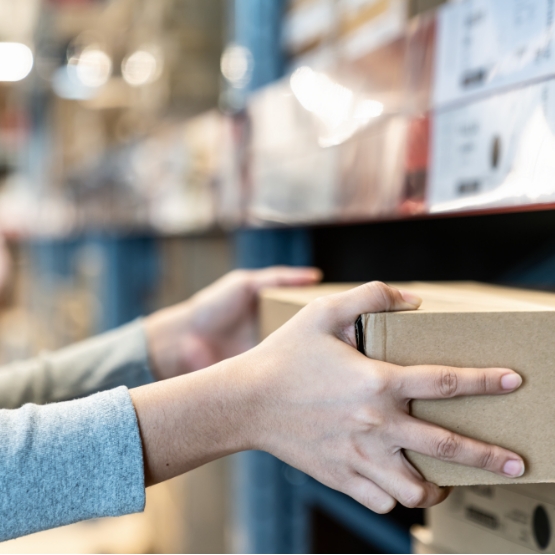
The Solution
Re-Think the Process
Our client's existing picking process was engineered to have each order picked into large totes and then sent to another area for packout and shipping. By integrating modules form the DCX Software Suite with their existing WMS, we developed a process that significantly reduced the use of the totes and streamlined the operation.
By re-engineered the order-picking process, installing intelligent software and upgrading other systems, workers can now pick items for the small orders directly into properly-sized shipping containers - eliminating labor costs, reducing conveyor congestion and freeing up valuable space in the warehouse.
Employ Intelligent Software
Next, we integrated DCX Software Suite's Cubing Module to review the items in each order and calculate the optimal shipping container. This greatly improved productivity as packers no longer had to guess how to pack orders and reduced the dimensional weights of most orders.
The Results
Once completed and running, a post-case analysis revealed that the savings from these improvements exceeded one million dollars. Our client not only realized a dramatic reduction in shipping and labor costs, but by picking directly into the shipping containers, it significantly increased the speed in which orders could be processed which reduced lead-times and improved customer satisfaction.
DCX Cubing System adjusts box sizes to accommodate dim weights.
The need for storing totes and shipping containers is eliminated.
Post-Case Anyalysis reveals shipping savings by over a million dollars.
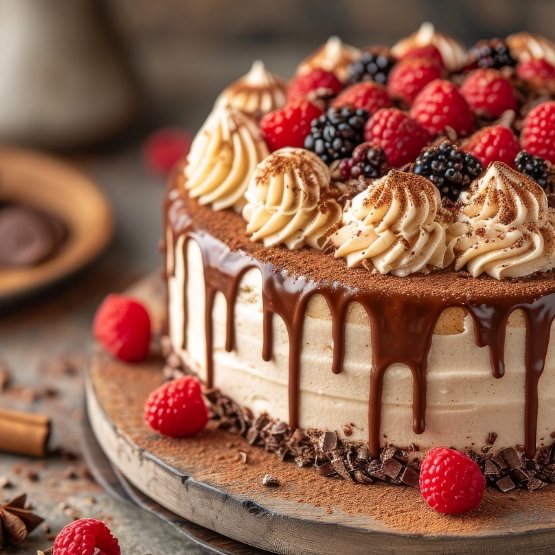
A Long-term Partnership
MMCI Order Fulfillment continued to work with this client to identify other areas for ongoing improvement like the installation of an automated box building machine and other warehouse automation processes.
"We partnered with MMCI Order Fulfillment to rethink our current processes because we trusted in their abilities to help us implement a solution that would increase the efficiency of our operation at the lowest possible cost."