KISS
Complete Warehouse Design and Automation Project
Since its founding over 30 years ago, KISS has become one of the dominant players in the cosmetics industry. They ship their products to over 50,000 mass retail locations across the US, thousands of beauty supply stores, and offer direct to consumer sales through their website.
The Challenges
While KISS faced the normal challenges associated with shipping more quickly, more accurately and more cost-effectively, these challenges were exacerbated by the fact that this new warehouse would service three totally different type of customers.
“The Omnichannel Fulfillment Challenge”
1. Big Box Retailers
While the big box retailers typically ordered in very large quantities and shipped full pallet loads, each store’s orders needed to be packaged for cross-docking at the distribution center. So, KISS had to pick, pack and pull orders as if each store location was an individual order.
2. Independent Beauty Supply Stores
In addition, the big box retailers, KISS supplied thousands of independent stores that ordered in both full and broken cases and shipped via a wide variety of trucking and delivery services.
3. Direct-to-Consumer Orders
Finally, KISS also fulfilled orders derived from the company’s online store – typically very small orders for individual items - with short lead times shipped via UPS, FEDEX or the U.S. Postal system.
Matched Picking Technology and Areas to Order Volumes
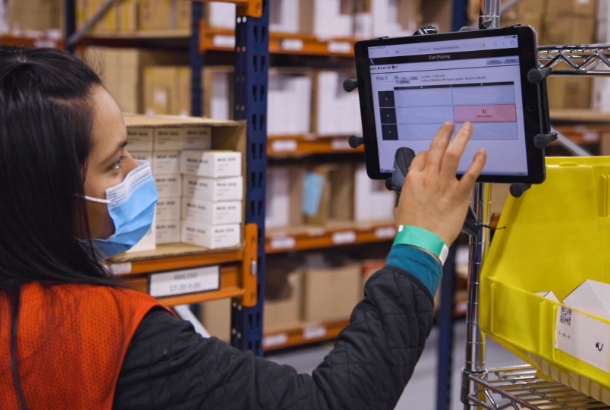
Slow-Moving Products
Integrated an intelligent cart picking process where multiple orders can be picked at the same time and then transferred to a tote that is conveyed to other parts of the system.
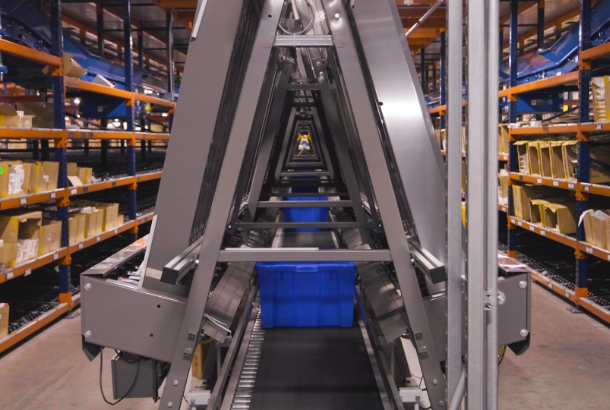
Fast-Moving, Small Products
Utilized highly efficient A-Frame dispensing technology for fast-moving products in smaller packages.
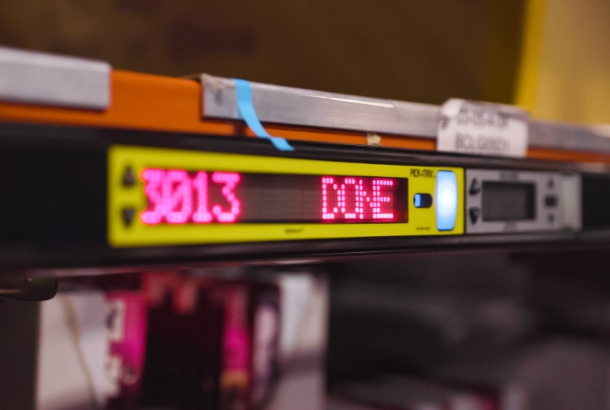
Medium/Fast-Moving Products
Installed pick-to-light technology, sorting conveyor and various controls to ensure the efficient picking of medium and fast-moving products that could not utilize the A-Frame dispensing system.
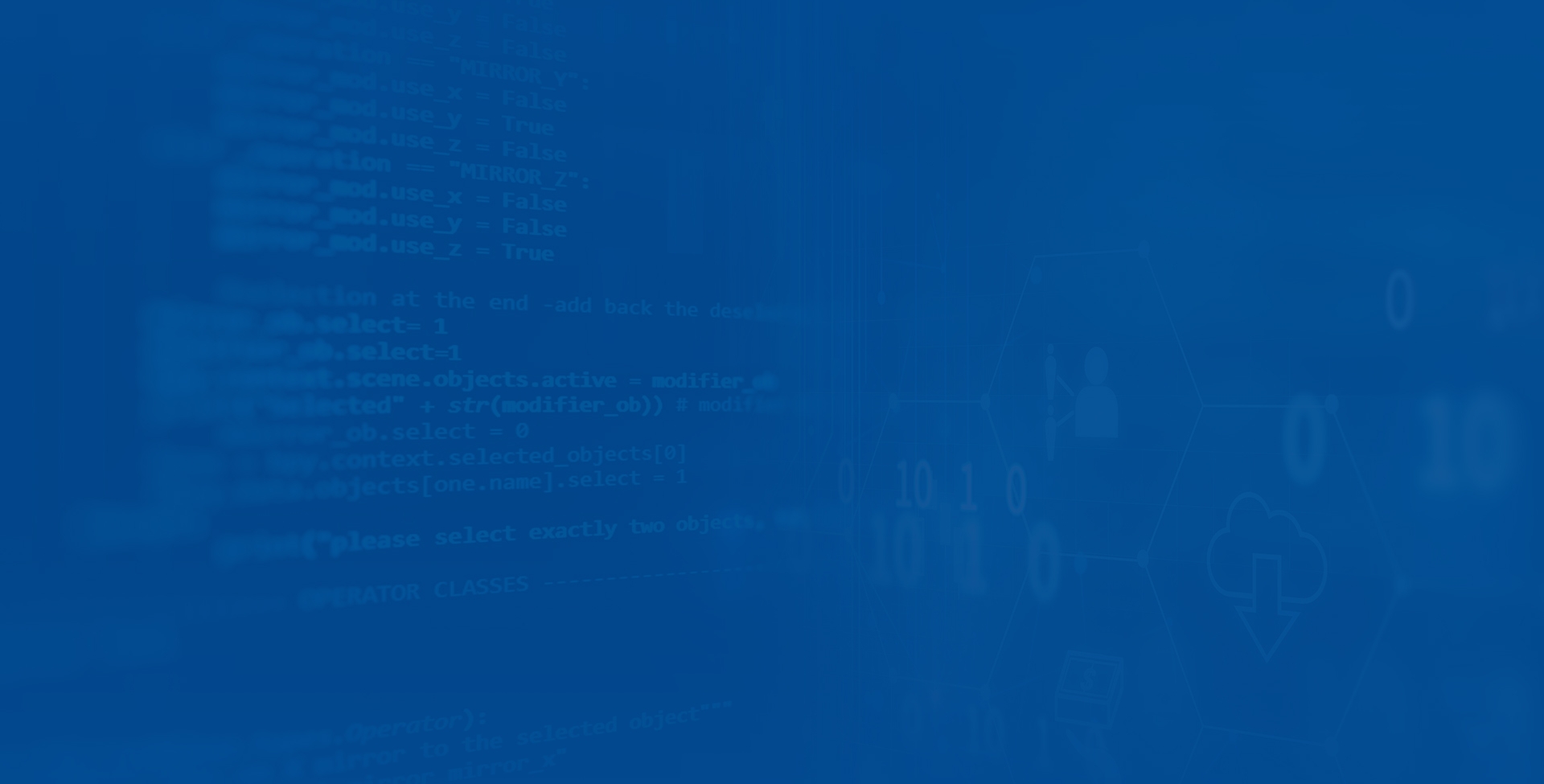
Integrated the Software and Controls
To integrate multiple technologies and multiple processes, our team also had to install and program the software to tie everything together. To achieve optimal performance, we installed our DCX Inventory and DCX Sort modules to sync data from KISS’s existing ERP system and guide the dynamic replenishment, movement and sorting of inventory.
DCX Inventory
DCX Sort
We then used our Order Management and Pick modules to automate the entire order process – from picking to packing – with a focus on balancing workloads, improving pick rates and reducing cycle times.
DCX Order Management
DCX Pick
DCX Pack
Finally, we integrated our DCX Pack Module to ensures containers were selected, packed, and checked in an efficient and effective manner. This software determines the most economical way to ship – both service level and what carrier to use – and then weighs the carton in line, automatically print and applies the shipping label and then route it to the proper shipping destination for parcel or palletizing.
The Results
While we remain focused on ongoing improvement, KISS is already seeing the benefits of using a single-source automation supplier whereby the design, software and controls are intelligently interconnected.